Ultonium® II glass lining with Microban® has a lower clay content than Ultonium® with Microban® which allows it to bond to high carbon pipe linings. As a premium glass lining, our cobalt blue Ultonium® II with Microban® offers special advantages.
Ultonium® II Glass Lining with Microban®
- Ideal for pipe used in chemical and latex paint processes
- Allows process temperatures to 350 degrees F
- Helps prevent the growth of bacteria, mold and mildew on the surface of the tank lining
- Formulated with special bonding agents to be amenable to both steel and ductile iron, developing a strong chemical bond between the glass and substrate during the fusing operation
Ultonium® II glass lining with Microban® is a multi-coat system achieving a finished thickness of 12 mils nominal. It is inspected visually and by spark test to ensure that the glass lining is free of pin holes crazing and scaling that would substantially expose the metal surface. Multiple layers of Ultonium® II glass lining with Microban® can be applied for additional wear and protection.
Requirements for the usage of Ultonium® II glass lining with Microban®
- The Ultonium® II glass lining with Microban® chemical bond shall be sufficient to permit a strain in the metal of .001 in. sq. (the yield point of carbon steel) without damage to the glass.
- Ultonium® II glass lining with Microban® will be applied to all wetted surface areas. The Ultonium® II glass lining with Microban® will subsequently be fired in a specially designed furnace at a maturing temperature in excess of 1600° F for the appropriate time to achieve a smooth vitreous lining, with a proper molecular bond.
- Warpage: During firing and after removal from the furnace, all piping will be supported to minimize the effects of warp age / deflection. As support does not control the expansion / contraction of the metal, the following parameters apply to the finished product. Applying a plum line from the pipe O.D. © the back of the flange on each end, the maximum deflection from plum will be as follows: Pipe from 1’0″ to 9’11” – 1/4″ Pipe from 10’0″ to 13’11” – 5/16″
- Ultonium® II glass lining with Microban® will have a hardness of at least 5.0 on the Mohs Scale, and a density of approximately 2.5 grams / cubic centimeter, as measured by ASTM designation D-792.
- Flanging of pipe and fittings will be accomplished by ASME certified welders and will conform to ASME accepted welding procedures. Connections will be std. 150 lb. slip-on or weld neck flanges, or machined stub ends, with 150 lb. class forged steel split back-up flanges.
- Causes for Rejection Arising from Fabrication:
- Flanges not perpendicular
- Bolt holes not aligned
- Fractures in welds
- Non sealing joints
- Damaged glass as a result of fabrication
- Care in Handling Glass Lined Steel Pipe & Fittings:
- Never lift by inserting solid device (i.e. tow motor fork) into barrel of item
- Never support entire weight of pipe or fittings on a single flange during Installation
- CRT-NA gaskets should be used with any glass lined pipe or fittings with glass applied to the flange faces, and should be loosened and re-torqued after a 24 hour heat cycle, to assure proper seating.
- Bolts must always be tightened in diametric opposition. When using CRT-NA gaskets, always conform to the following torque values (ft. lbs.):
- 1″ = 20 – 30#
- 2″, 3″ & 4″ = 30 – 50#
- 6″ & 8″ = 50 – 90#
- 10″ & 12″ = 75 – 125#
- Never hammer joints into place
- In storage, never support the item directly on the glass of a flange face
- In process, glass lined pipe should be supported by cradles or slings with at least 1 per every 6’ of horizontal run. Vertical runs of pipe should be equipped with the appropriate base expansion joints, and intermediate stabilizers, especially on sections in excess of 10’. Anchoring pipe properly at each side of an expansion joint system permits adjustment, and allows for the isolation of vibration.
Niles Ultonium® II with Microban® is rigidly tested under the following ASTM testing guidelines:
W-H-196 Test = 7.0 – 8.0 mg/in2 — This test consists of exposing the enamel to a boiling (212 F) 4/10% solution of sodium Bicarbonate for (8) eight, (18) eighteen-hour cycles. Maximum weight loss after eight cycles is not to exceed 15 mg/in2.
PEI T-21 Spot Acid Test — This test is used to determine enamel resistance to acids. The test area is examined for visible effects on the enamel and is graded from Class AA (no sign of etching) to Class D (etched surface). NST’s Ultonium® II glass lining with Microban® records Class A performance, equating to excellent chemical resistance.
Impact resistance = Class 4 to 5 — The impact resistance test is used to determine the adhesive qualities of enamel to the substrate. The enamel is graded on the fractured glass’s ability to maintain its adherence in the impact area (an actual indication of the chemical bond). With Class 1 being the worst to Class 5 the best, Class 3 is considered acceptable. NST’s Ultonium® II glass lining with Microban® outstanding strength performance consistently falls between the upper Class 4 and middle Class 5 range.
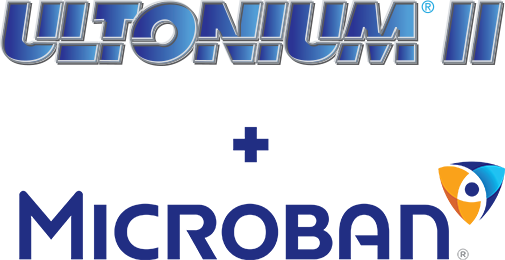
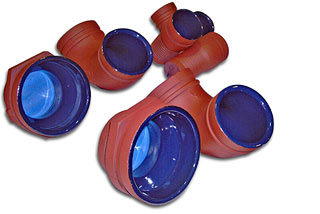